
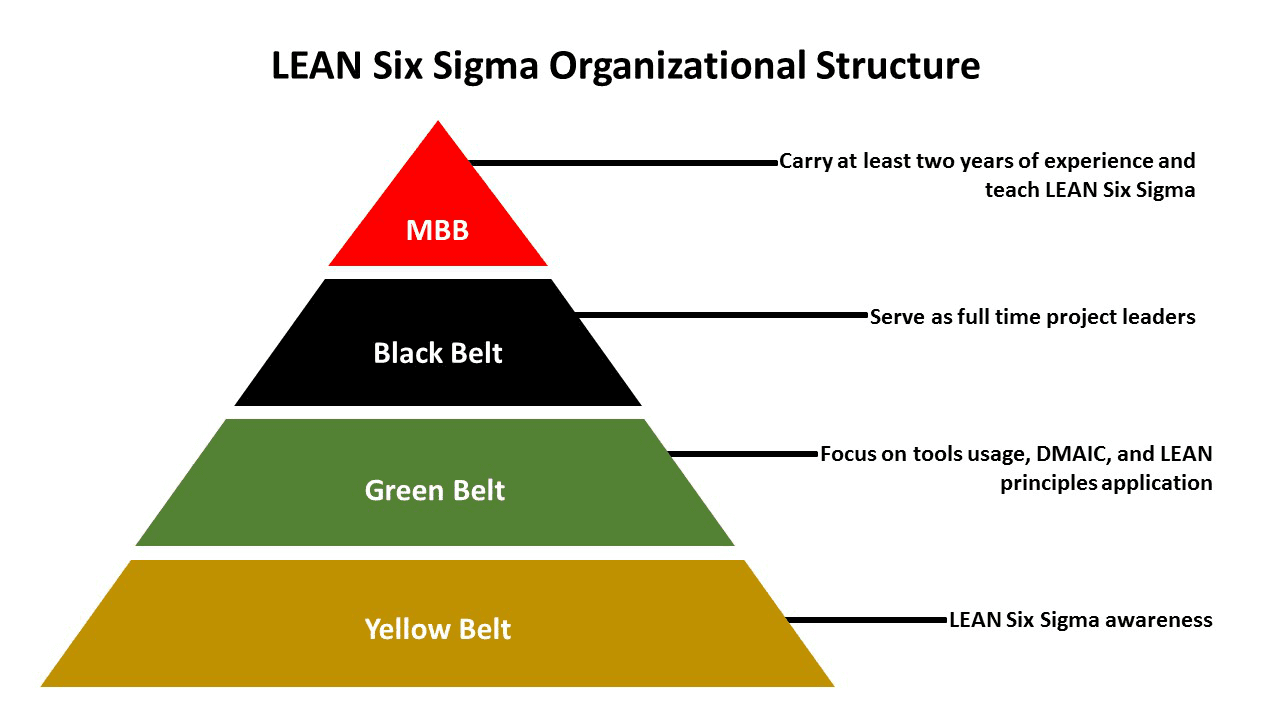
At Jabil, Lean Six Sigma is not merely a “flavor of the month.” It permeates how we operate daily and is part of our DNA. While some business approaches are short-lived trends, Lean Six Sigma has stood the test of time and remains more relevant than ever. Creating a Culture of Operational Excellence with Lean Six Sigma The true goal of this approach should always be to deliver operational excellence. Waste reduction is a cost and time-saving endeavor, but it is just one piece of a holistic Lean Six Sigma strategy. A “six sigma” process occurs when no defects are expected in 99.99966% of all chances to produce them.
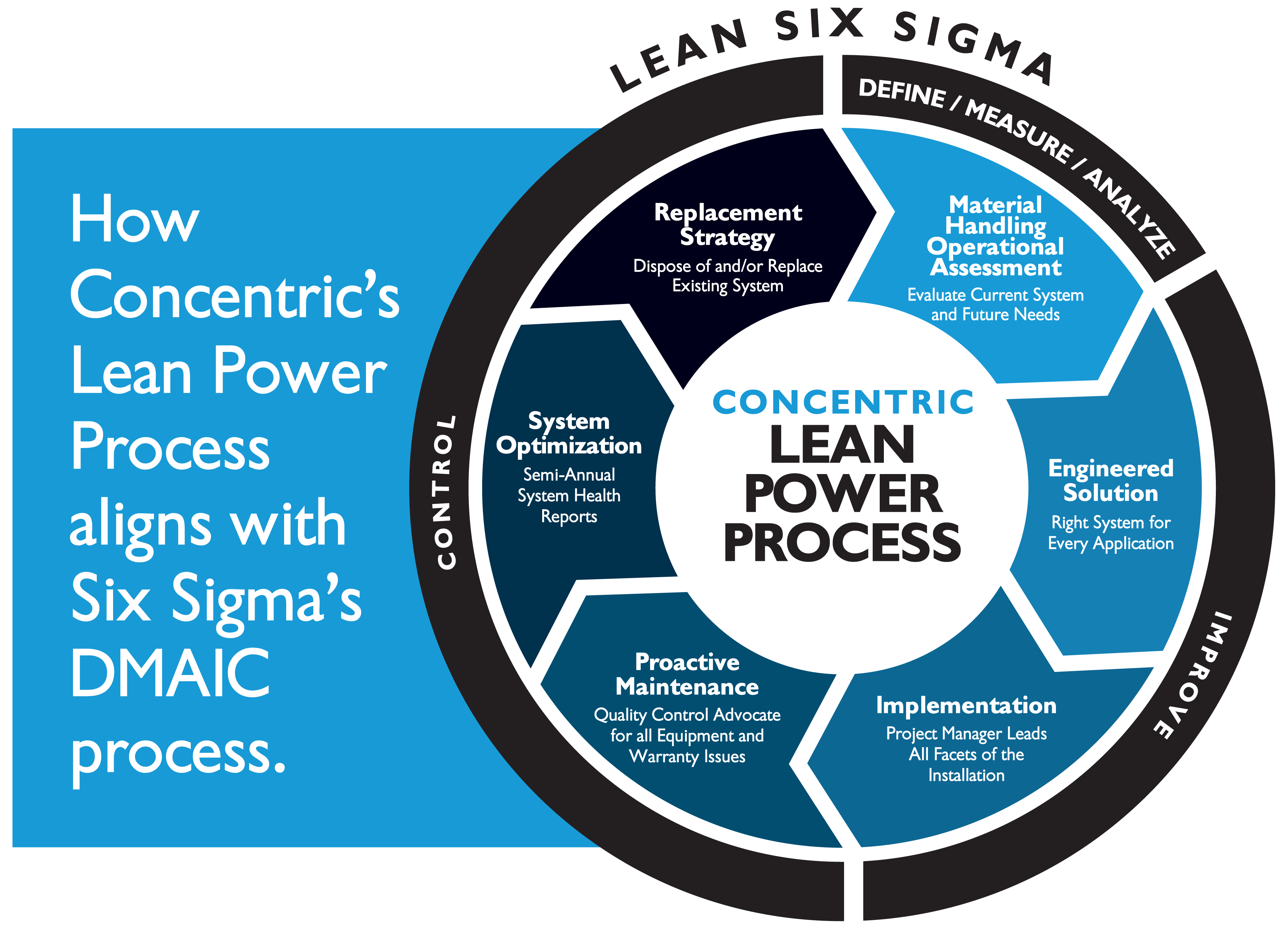
Rooted in the scientific method of problem solving, the main objective of any Six Sigma implementation is quality improvement through the reduction of variation and defect rates in production processes. Lean is a way of thinking about creating value by analyzing processes to eliminate waste and make workflows more efficient. Lean Six Sigma combines the mindsets and methodologies of problem-solving from Lean and Six Sigma to create a complementary system that delivers a deeper look into maximizing customer value while reducing waste. At Jabil, we’ve embedded Lean Six Sigma methodologies into our culture and leadership in order to ensure that the people we work with and those we serve consistently receive our absolute best. For Jabil, this is already our default mode of operation, with a global Lean Six Sigma team dedicated to creating and fostering a workforce of problem solvers, where employees are focused on continually driving improvements in quality, delivery and cost.īut it’s not just about our output. Manufacturers and technology providers that strive for zero defects and the elimination of waste are poised to meet these challenges head on. Now more than ever, your organization needs business partners that are committed to quality, efficiency and cost-effective production. Rising prices of goods and transportation. Labor shortages from workforce turnovers and health-related absences.
